Bruder Piggyback Forklift Build part 3
In this part I'll show how I assembled the steering and drive motor assembly. I used a common N20 motor/gear box. The one I used was rated 12V and 100rpm. I used a 12V rated motor because I initially was going to use a 3S LIPO battery and ESC.
If you haven't already you need to print out the 'UPS_drive_motor_arm' from the Thingiverse files. The N20 motor was a perfect friction fit in mine and required nothing else to hold it in place. Sorry, don't have a photo just showing how the motor fits into the arm but it's pretty obvious once you see the part.
There is a recess in the top of the arm that fits over the shaft of the servo and a standard servo arm screw is used to secure it in place.
I had a problem with the arm slipping on the servo and not staying in place. To fix this I put the arm in my small milling machine and cut a flat bottom hole with a 1/4in cutter.
[img]
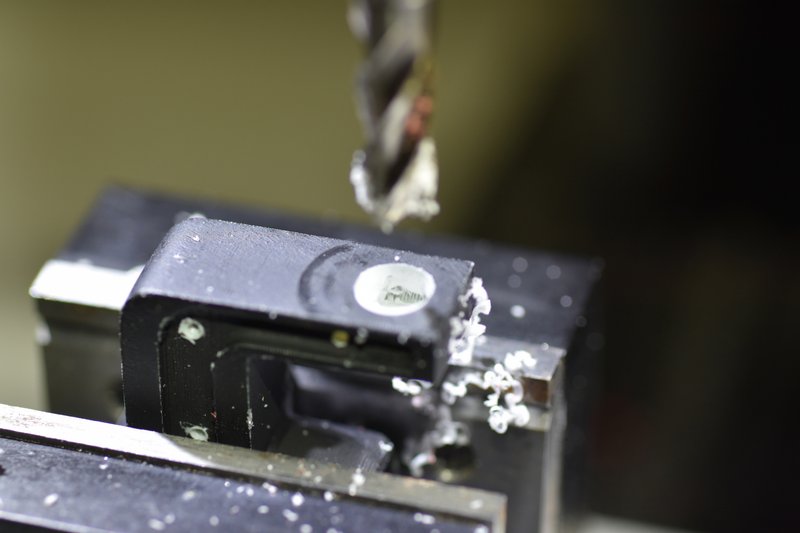
[/img]
I then took an old, damaged servo arm I had and cut the center splined hub out and epoxied it into the hole I just milled.
[img]
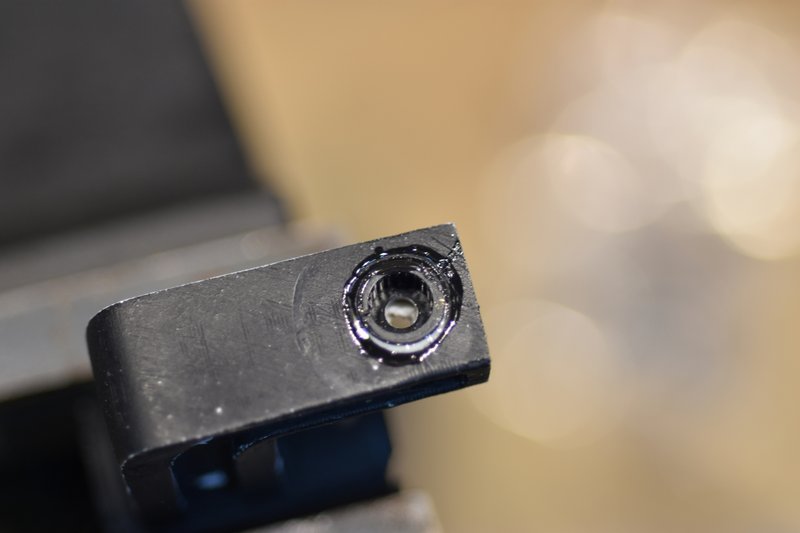
[/img]
This locks the arm to the servo shaft and no more slipping.
Next was to mount the wheel/tire to the motor shaft. The shaft from the gear box is 3mm in diameter and is a loose slip fit into the hole in the hub of the wheel. The hub though is longer than the motor shaft so that when placed on the drive shaft the tire is not centered under the servo shaft. To fix this the hub has to be shortened. To determine how much to remove I took a thin piece of plastic, placed it alongside the motor shaft and marked it to use a length gauge.
[img]
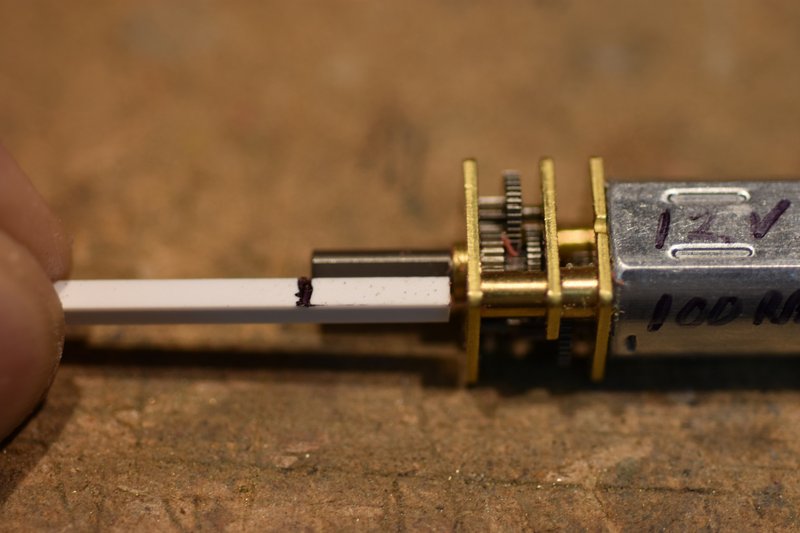
[/img]
There are a number of ways to cut back the hub, I used my small mill after clamping up the wheel/tire in a 3-jaw chuck.
[img]
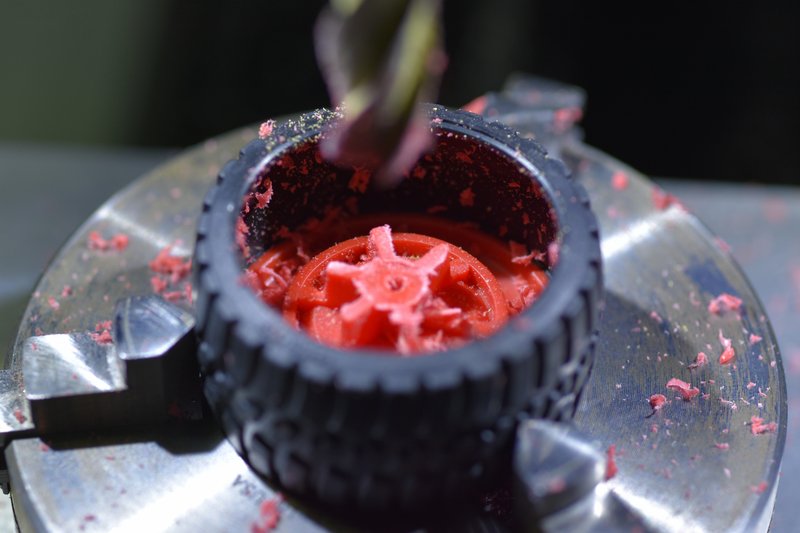
[/img]
Then I would mill off a little bit of the hub, check the remaining length with the gauge. Kept repeating this until the mark on the gauge was fully exposed.
[img]
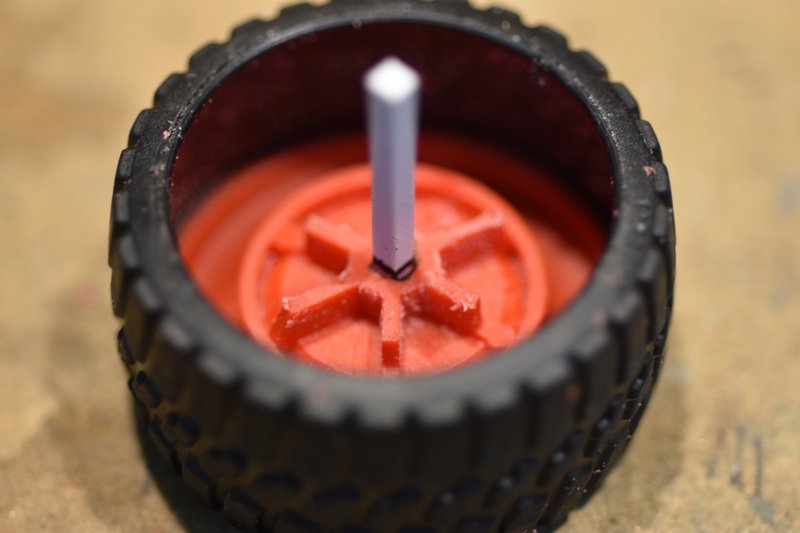
[/img]
This ensured that the remaining hub was just slightly shorter than the length of the motor shaft and would not rub against the gear box. The tire ended up being almost completely centered under the servo shaft. It's just a little off but not enough to be a problem. If you want it to be completely centered then you could remove a little bit off the end of the drive shaft and shorten the hub just a little more. If you try and drill the hub a little deeper I think you have a good chance of just drilling right through the front of the hub which would ruin the looks. I didn't think it was worth the bother to do.
As mentioned above the motor shaft is a loose fit into the wheel hub. Since the original axle was pretty much a friction fit I figured that would work here as well. There is a flat on the motor shaft and I used CA to secure a thin strip of styrene on it.
[img]
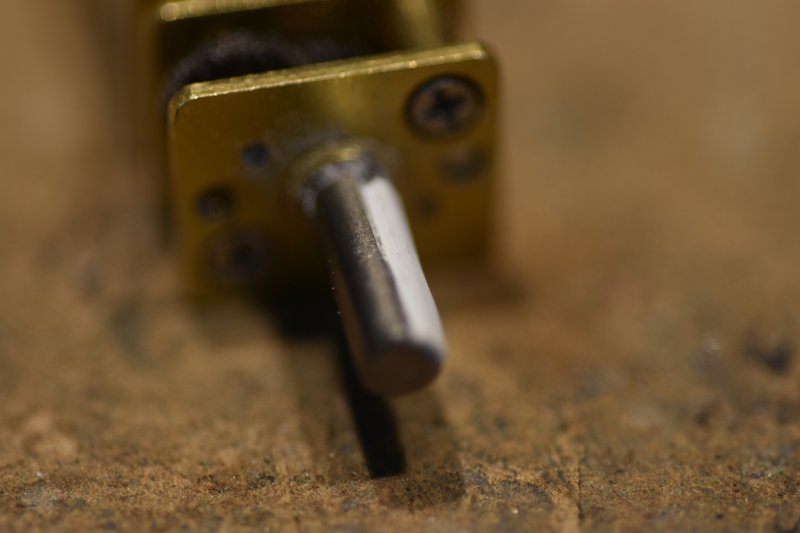
[/img]
After the glue cured I carefully sanded the plastic down until I got a nice snug fit of the hub over the drive shaft.
[img]
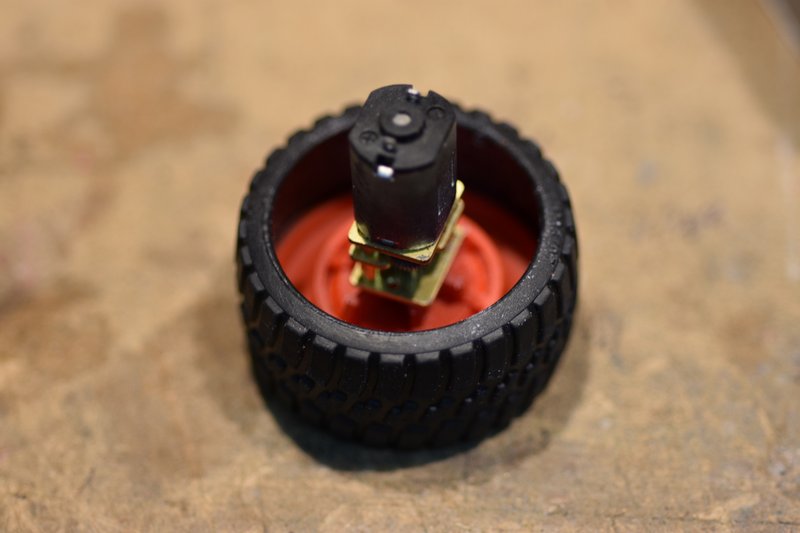
[/img]
Soldered the power wires to the motor and inserted the motor into the support arm.
[img]
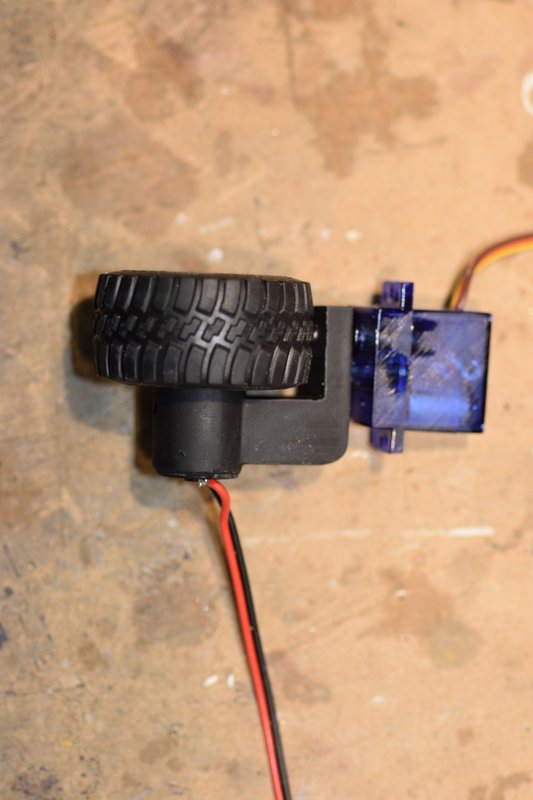
[/img]
On one side of the support arm is a groove. I used this to route the power wires around the back side of the arm. To hold the wires in place I used a few tiny eye screws. These are used to hang pictures and are available in craft stores.
[img]
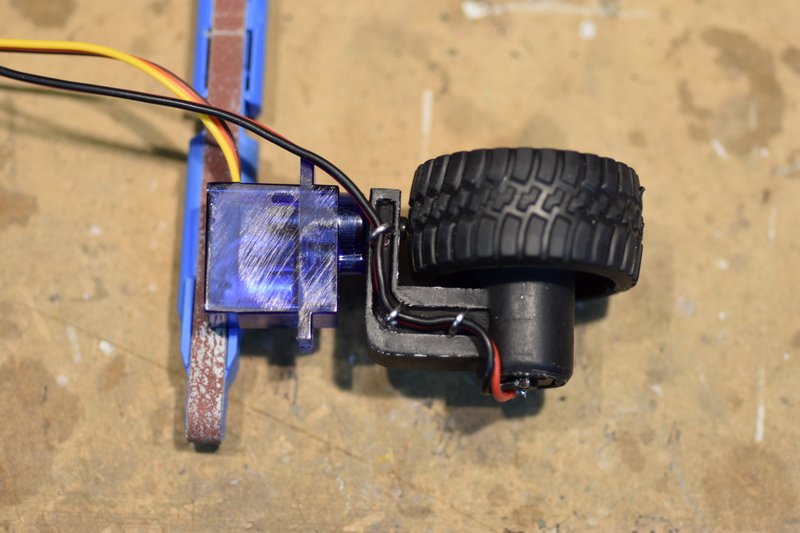
[/img]
I then installed the assembly into the mounting plate installed earlier. The servo has to be inserted from the bottom at an angle and then rotated into final position. I was able to do this as a complete assembly but you could also just insert the servo first and then attach the arm and then insert the motor
[img]
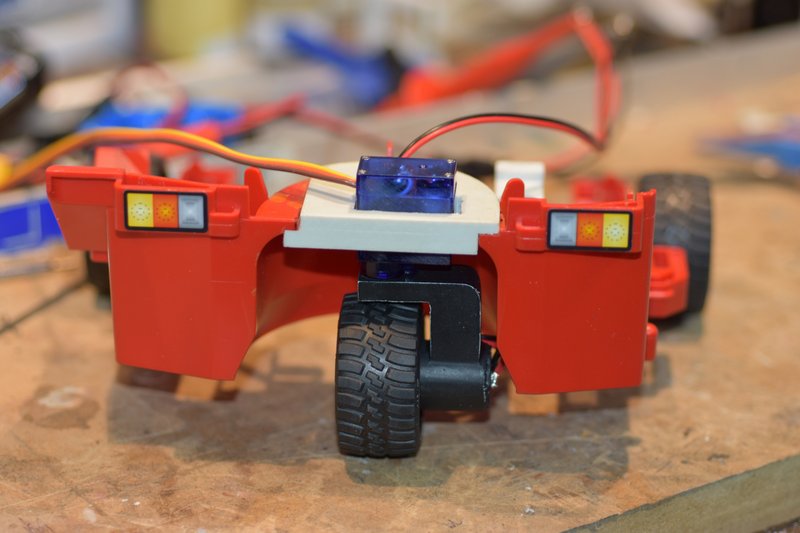
[/img]
Next was to hook it up to a battery and receiver and test the functioning. It worked well but only turned 90 degrees left and right. Well that's the 'normal' range of motion on typical servos. The real world forklifts like this though are capable of ZTR or Zero Turn Radius. That's what I wanted for this model also. The classic fix to get more rotation is to take the servo apart and insert a couple of resistors into it's potentiometer circuit. Yea, that's a pain to do in a standard size servo. I really didn't want to try on a micro servo like this. Fortunately I was using a new Radiomaster TS16S transmitter for this build. It allows me to extend my endpoints out to 150% so I could get more servo rotation without having to modify the servo. It won't get me all the way to a full 180 degrees but it's close enough.
[img]
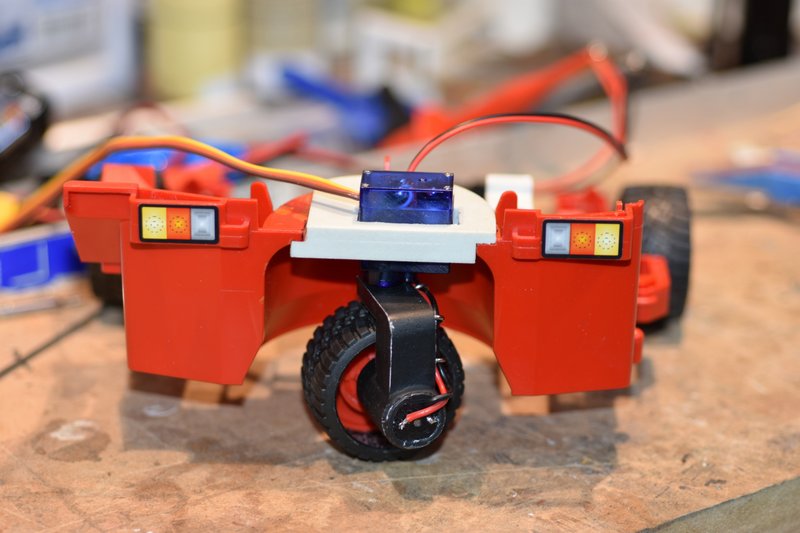
[/img]
[img]
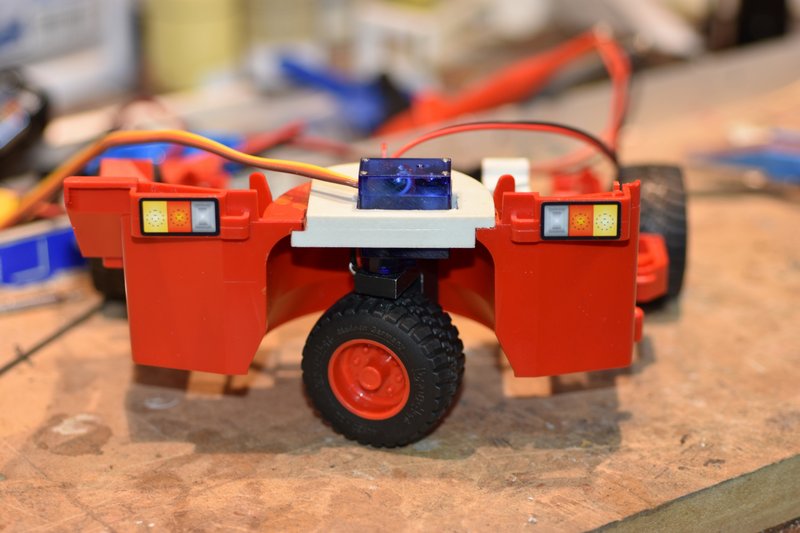
[/img]
That's all for this post. In the next I'll start in on the lift mast.